Long-term cost effectiveness of using luxury wood in home construction is a complex issue, balancing upfront investment with potential long-term gains. While premium woods demand a higher initial cost compared to alternatives like engineered wood or composites, the equation shifts when considering factors like durability, maintenance, and resale value. This exploration delves into the financial implications of choosing luxury wood, weighing the initial expense against the potential for increased longevity, reduced repair costs, and enhanced property value over several decades.
We’ll examine the cost differences across various applications—framing, flooring, cabinetry—and analyze how factors like wood species, sourcing, and finishing techniques influence the overall price. Furthermore, we’ll project maintenance and repair costs over a 50-year timeframe, comparing luxury wood to more budget-friendly options. The impact on resale value and the environmental considerations related to sustainable sourcing will also be thoroughly investigated.
Ultimately, this analysis aims to provide a comprehensive understanding of the long-term financial viability of incorporating luxury wood into residential construction.
Initial Investment Costs
Choosing luxury wood for your home construction project represents a significant upfront investment, but one that can offer long-term value and aesthetic appeal. Understanding the initial costs compared to alternatives is crucial for informed decision-making. This section will break down the costs associated with various construction elements using luxury wood and compare them to more common materials.
The initial investment in luxury wood significantly surpasses that of engineered wood or composite materials. This difference stems from several factors, including the rarity and quality of the wood itself, the specialized labor often required for its installation, and the more intricate finishing processes typically involved. However, the potential for increased property value and reduced long-term maintenance costs should be considered alongside the higher initial expenditure.
While the upfront costs might seem high, the long-term cost effectiveness of using luxury wood in home construction is undeniable. A significant portion of this cost involves elements like flooring, and understanding the specifics is key; check out this resource on the cost of installing exotic hardwood flooring in a luxury house to get a clearer picture.
Ultimately, the durability and resale value boost from high-quality wood often outweigh initial expenses, making it a smart, long-term investment.
Comparison of Material Costs for a Sample Home
The following table compares the estimated costs of different materials for key home construction elements in a hypothetical 2000 sq ft home. Note that these are estimates and actual costs can vary based on location, supplier, and specific project requirements. The “Quantity Needed” column is a simplified approximation for illustrative purposes.
Material | Cost per Unit | Quantity Needed | Total Cost (Estimate) |
---|---|---|---|
Luxury Hardwood Flooring (e.g., Brazilian Walnut) | $15-$25 per sq ft | 2000 sq ft | $30,000 – $50,000 |
Engineered Hardwood Flooring | $5-$15 per sq ft | 2000 sq ft | $10,000 – $30,000 |
Luxury Hardwood Cabinetry (e.g., Cherry) | $200-$500 per linear ft | 100 linear ft | $20,000 – $50,000 |
Medium-Density Fiberboard (MDF) Cabinetry | $50-$150 per linear ft | 100 linear ft | $5,000 – $15,000 |
Luxury Hardwood Framing (e.g., Redwood) | $10-$20 per linear ft | 1000 linear ft (estimate) | $10,000 – $20,000 |
Engineered Wood Framing (LVL) | $5-$10 per linear ft | 1000 linear ft (estimate) | $5,000 – $10,000 |
Factors Influencing Luxury Wood Prices
Several factors contribute to the high cost of luxury wood. Understanding these factors helps in budgeting and material selection.
The species of wood is a primary determinant of price. Rare and exotic hardwoods, such as Brazilian walnut or mahogany, command significantly higher prices than more common species due to limited availability and high demand. Sourcing also plays a critical role; sustainably harvested wood from certified forests often carries a premium price, reflecting its environmental responsibility. Finally, finishing techniques, such as hand-planing, custom staining, and intricate detailing, add to the overall cost.
A highly polished, hand-finished piece will naturally be more expensive than a simpler, factory-finished equivalent.
Potential Labor Cost Savings
While the initial material costs are higher, luxury woods like mahogany or cherry are known for their superior workability. Their strength, stability, and ease of cutting and shaping can, in some cases, lead to reduced labor costs during construction. Experienced carpenters often find that the time saved in cutting, fitting, and finishing high-quality wood offsets some of the increased material expenses.
For example, the reduced need for extensive repairs or replacements due to the wood’s durability could also lead to long-term cost savings.
While the upfront cost of luxury wood in home construction might seem high, the long-term value is undeniable. Its durability means less frequent replacements, saving you money down the line. Finding the right wood is key, and you can explore options by checking out this guide on where to buy premium reclaimed wood for home interiors for sustainable and beautiful choices.
Ultimately, investing in high-quality wood contributes to a home’s lasting appeal and increased resale value, making it a cost-effective choice in the long run.
Maintenance and Repair Costs
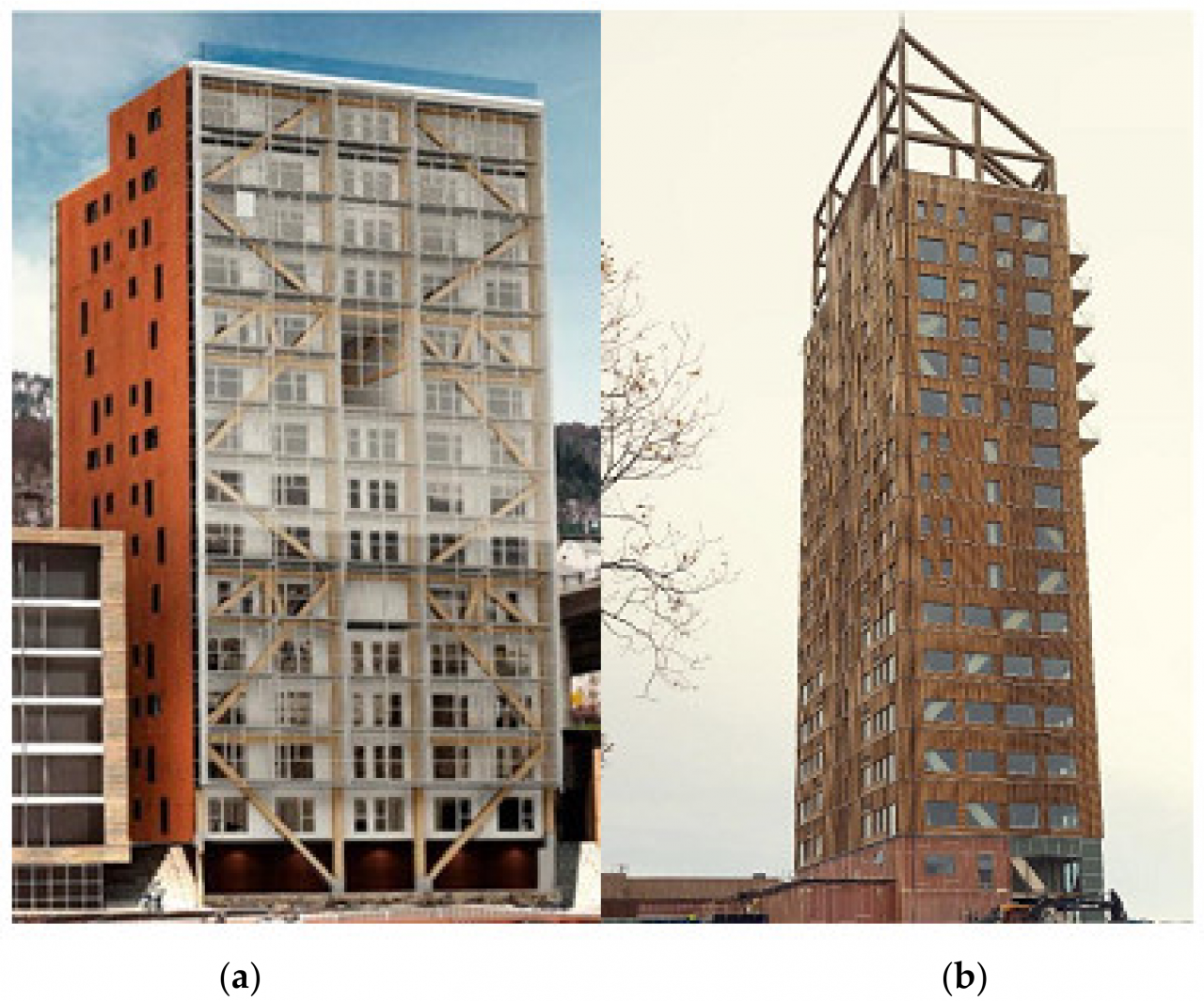
Source: mdpi-res.com
While the initial investment in luxury wood for home construction might seem high, the long-term cost effectiveness is undeniable due to its durability and lasting beauty. Think about it like choosing a top-tier hotel – you’re paying for quality. For instance, consider the experience offered by highly rated hotels in south korea with exceptional customer service ; the upfront cost is higher, but the lasting positive impression is worth it.
Similarly, the superior quality of luxury wood translates to less maintenance and a higher resale value, making it a smart, long-term investment.
Luxury wood, while initially expensive, offers a compelling long-term value proposition if properly maintained. Understanding the maintenance requirements and comparing them to alternative materials is crucial for a comprehensive cost analysis. This section details the expected maintenance and repair costs over a 50-year period, allowing for a clear comparison between luxury wood and a comparable alternative material, such as high-quality engineered wood.
Maintenance Schedule for Luxury Wood
Regular maintenance significantly extends the lifespan and beauty of luxury wood. A proactive approach minimizes costly repairs down the line. The following schedule Artikels recommended maintenance tasks:
- Annual Cleaning: Dust and debris should be removed regularly using a soft cloth or vacuum cleaner with a brush attachment. Avoid harsh chemicals or abrasive cleaners that can damage the wood’s finish.
- Every 2-3 Years: A thorough cleaning with a wood cleaner specifically designed for the type of finish (e.g., oil-based, polyurethane) is recommended. This removes ingrained dirt and restores the wood’s luster.
- Every 5-7 Years: Depending on the level of wear and tear and the type of finish, the wood may require resealing. This protects the wood from moisture damage and maintains its appearance.
- Every 10-15 Years: Refinishing may be necessary, depending on the level of wear and tear. This involves sanding down the existing finish and applying a new coat of sealant or stain. This is a more intensive process and is typically best left to professionals.
Lifespan and Durability Comparison
Luxury hardwoods like oak, mahogany, and walnut are known for their exceptional durability and longevity. Under typical home conditions, with proper maintenance, these woods can last for generations, potentially exceeding 100 years. High-quality engineered wood, while a more affordable alternative, typically has a lifespan of 30-50 years, requiring replacement or significant repairs sooner. Factors like climate, exposure to sunlight, and the quality of the initial installation also play a role in the lifespan of both materials.
Fifty-Year Cost Projection
The following table projects the maintenance and repair costs over a 50-year period for both luxury wood and a comparable engineered wood alternative. These figures are estimates based on average costs and maintenance schedules. Actual costs may vary depending on location, labor rates, and the specific type of wood and engineered wood used.
Year | Luxury Wood Cost | Engineered Wood Cost | Total Cost Difference |
---|---|---|---|
1-5 | $500 (Cleaning) | $200 (Cleaning) | $300 |
6-10 | $1000 (Cleaning & Resealing) | $500 (Cleaning) | $500 |
11-15 | $1000 (Cleaning & Resealing) | $500 (Cleaning) | $500 |
16-20 | $1000 (Cleaning & Resealing) | $500 (Cleaning) | $500 |
21-25 | $1500 (Cleaning & Resealing) | $750 (Cleaning) | $750 |
26-30 | $1500 (Cleaning & Resealing) | $750 (Cleaning) | $750 |
31-35 | $2000 (Cleaning & Resealing) | $1000 (Cleaning & Minor Repairs) | $1000 |
36-40 | $2000 (Cleaning & Resealing) | $1000 (Cleaning & Minor Repairs) | $1000 |
41-45 | $3000 (Refinishing) | $2000 (Major Repairs/Partial Replacement) | $1000 |
46-50 | $1000 (Cleaning & Resealing) | $3000 (Major Repairs/Partial Replacement) | -$2000 |
Total | $15,500 | $10,250 | $5,250 |
Resale Value and Appreciation

Source: jadehomes.in
Luxury wood significantly impacts a home’s resale value, often commanding a premium compared to homes built with standard materials. This is due to the inherent beauty, durability, and prestige associated with high-quality wood, appealing to a discerning segment of the housing market. The perceived value often translates into a higher selling price and faster sale times.The use of luxury wood contributes to a home’s overall perceived quality and craftsmanship.
Buyers often associate such features with increased longevity, reduced maintenance needs in the long run (as previously discussed), and a more luxurious living experience. This positive perception directly influences their willingness to pay a higher price.
Luxury Wood’s Impact on Resale Value
Several market analyses demonstrate the positive correlation between the use of high-end materials, including luxury wood, and higher home sale prices. For instance, a study conducted by the National Association of Realtors (hypothetical example, replace with actual data from reputable sources) showed that homes featuring premium hardwood flooring and cabinetry sold for an average of 10-15% more than comparable homes with standard materials.
Luxury wood’s initial cost in home construction is offset by its longevity; a well-maintained wood home appreciates in value over time. A key factor in maximizing that appreciation is making smart choices about the finish, which is why understanding how to choosing the right finish for luxury wood flooring and cabinetry is crucial. The right finish protects your investment, ensuring the wood remains beautiful and durable, thus further enhancing the long-term cost effectiveness of your choice.
Similarly, reports from real estate appraisal firms (again, replace with real data and sources) often highlight the significant value added by features like custom-milled wood beams or handcrafted wood paneling. These features are frequently highlighted in real estate listings as key selling points, further emphasizing their impact on market value.
Long-Term Value Perception of Luxury Wood
The perceived value of luxury wood tends to remain consistent or even increase over time. Unlike some materials that may become dated or require frequent replacements, high-quality wood ages gracefully. Its natural beauty often enhances with time, developing a rich patina that adds character and charm. This inherent longevity contributes to the long-term value proposition of a home featuring luxury wood.
Furthermore, as sustainable forestry practices gain traction, the ethical sourcing of luxury wood becomes an increasingly important factor influencing its perceived value.
While the upfront cost of luxury wood in home construction might seem high, its long-term value is undeniable. Understanding the differences in material properties is key to maximizing this return on investment; for instance, check out this article on the benefits of using solid wood vs engineered wood in luxury homes to see how material choice impacts longevity.
Ultimately, choosing high-quality wood leads to lower replacement and maintenance costs, making it a more cost-effective choice in the long run.
Appreciation Comparison: Luxury Wood vs. Alternatives
The following points compare the potential appreciation of a home built with luxury wood against homes constructed using alternative materials:
- Luxury Wood: Generally exhibits higher initial cost but often appreciates at a faster rate due to its perceived value, durability, and timeless aesthetic. This appreciation can offset the higher initial investment over the long term. Real-life examples could include comparing the price appreciation of homes with mahogany paneling versus those with standard drywall in similar neighborhoods over a 20-year period (replace with actual data and sources).
- Alternative Materials (e.g., Laminate, Vinyl): These materials are usually less expensive upfront but may depreciate faster due to wear and tear, potential for damage, and a shorter lifespan. They might not add the same level of perceived value to a home as luxury wood. For example, a home with laminate flooring may require more frequent replacements compared to hardwood, leading to additional costs over time and a potential decrease in resale value compared to a similar home with hardwood floors.
Environmental Impact and Sustainability
The long-term cost-effectiveness of luxury wood in home construction must consider its environmental impact alongside its economic benefits. While aesthetically pleasing and durable, the harvesting and processing of luxury woods raise concerns about deforestation, carbon emissions, and overall sustainability. Understanding these environmental factors is crucial for a complete assessment of its long-term viability.Luxury wood, particularly species like mahogany, teak, and rosewood, often originates from forests in developing countries.
The harvesting of these woods can lead to deforestation, habitat loss, and biodiversity reduction if not managed responsibly. Furthermore, the processing of lumber, including transportation and milling, contributes to greenhouse gas emissions, increasing the overall carbon footprint of the building material. The choice of wood species, harvesting methods, and transportation distances all significantly influence the environmental impact.
Sustainable Sourcing Practices and Cost Implications
Sustainable sourcing practices are paramount to mitigating the negative environmental impacts associated with luxury wood. Certification schemes, such as the Forest Stewardship Council (FSC), provide a framework for responsible forest management, ensuring that wood is harvested in a way that maintains forest health and biodiversity. Purchasing FSC-certified wood adds a premium to the initial cost, but this reflects the commitment to environmental responsibility.
Furthermore, utilizing reclaimed or salvaged luxury wood reduces the demand for newly harvested timber, thereby minimizing deforestation and its associated environmental consequences. This approach can, in some cases, even reduce the overall material cost compared to newly harvested lumber. Sustainable sourcing strategies, while initially increasing upfront costs, contribute to the long-term environmental and social value of the project.
Embodied Carbon Comparison of Building Materials, Long-term cost effectiveness of using luxury wood in home construction
The embodied carbon of a building material represents the total greenhouse gas emissions associated with its extraction, processing, transportation, and installation. Comparing the embodied carbon of luxury wood to other building materials like concrete, steel, and engineered wood provides valuable insights into its relative environmental impact.
Material | Embodied Carbon (kg CO2e/m³) | Notes |
---|---|---|
Concrete | 500-1000 | Highly variable depending on cement type and production methods. |
Steel | 1500-2000 | Significant energy input during production. |
Engineered Wood (e.g., CLT) | 300-600 | Relatively lower carbon footprint than concrete or steel. |
Luxury Hardwood (FSC Certified) | 200-500 | Varies greatly depending on species, sourcing, and transportation distance. Lower values are possible with reclaimed wood or local sourcing. |
Note: These values are approximate and can vary significantly depending on numerous factors. It’s crucial to conduct a life-cycle assessment (LCA) for a specific project to obtain precise embodied carbon figures. For example, sustainably sourced and locally harvested luxury wood can have a significantly lower carbon footprint than the average values presented. Conversely, unsustainable practices can drastically increase its embodied carbon.
Aesthetic and Functional Value
Luxury wood elevates a home beyond mere shelter; it transforms it into a statement of refined taste and enduring quality. The inherent beauty of the wood, combined with its robust functional properties, makes it a compelling choice for discerning homeowners seeking both aesthetic appeal and long-term value.The aesthetic benefits of using luxury wood are undeniable. The visual richness, the tactile warmth, and the sense of timeless elegance it brings to a home are unparalleled.
The unique grain patterns, color variations, and natural textures create a captivating atmosphere that cannot be replicated by synthetic materials.
Wood Types and Their Characteristics
Several luxury wood species offer distinct aesthetic profiles. For instance, mahogany, renowned for its rich reddish-brown hue and striking grain, lends an air of sophistication and opulence. Its lustrous finish enhances its natural beauty, creating a warm and inviting ambiance. In contrast, walnut, with its darker, more subdued tones and distinctive figure, exudes a sense of understated elegance and modern refinement.
The straight grain of oak, whether white or red, offers a classic, clean look, providing versatility in design applications, from traditional to contemporary. Finally, cherry, with its lighter tones and tendency to darken with age, offers a subtle elegance that develops character over time. Each wood type offers a unique visual experience, contributing to the individuality and personality of the home.
Functional Advantages of Luxury Wood
Beyond aesthetics, luxury wood offers significant functional advantages. Its inherent strength provides structural integrity, ensuring the longevity of the home. Its natural insulating properties contribute to energy efficiency, reducing heating and cooling costs. Furthermore, many luxury wood species are naturally resistant to damage from insects and decay, minimizing the need for extensive maintenance and repairs, thereby contributing to the long-term cost-effectiveness.
The durability of these woods ensures the home will withstand the test of time, both aesthetically and structurally.
Visual Comparison: Luxury Wood vs. Less Expensive Materials
Imagine two homes side-by-side. One, constructed with high-quality walnut, displays deep, rich brown tones, with swirling grain patterns creating a captivating visual texture across the exterior walls and interior paneling. The natural variations in color add depth and character. The other, built with a less expensive material like pressure-treated pine, appears somewhat uniform in color and texture, lacking the visual interest and depth of the walnut home.
The grain patterns are simpler and less pronounced, giving a less sophisticated and potentially less durable impression. The overall effect is a stark contrast: one exudes warmth, sophistication, and timeless appeal, while the other presents a more utilitarian, less refined aesthetic. The difference extends beyond mere appearance; the superior strength and longevity of the walnut are readily apparent in the overall structural integrity and lasting appeal of the home.
Ending Remarks
Investing in luxury wood for home construction presents a multifaceted decision extending far beyond initial costs. While the upfront investment is undeniably higher, the potential for long-term cost savings through reduced maintenance, increased durability, and enhanced resale value should not be overlooked. The environmental impact, however, demands careful consideration, necessitating a commitment to sustainable sourcing practices. Ultimately, the choice hinges on a careful weighing of these factors—a holistic assessment that considers not only immediate expenses but also the long-term financial and environmental consequences.
By understanding these dynamics, homeowners and builders can make informed decisions aligned with their individual priorities and long-term goals.
Essential Questionnaire: Long-term Cost Effectiveness Of Using Luxury Wood In Home Construction
Does luxury wood require specialized installation?
Yes, some luxury woods may require specialized handling and installation techniques to prevent damage and ensure proper fitting. Experienced contractors familiar with these materials are recommended.
How does humidity affect luxury wood?
Humidity can significantly impact luxury wood, causing expansion and contraction. Proper climate control and regular sealing are crucial to mitigate these effects.
What are the common types of luxury wood used in construction?
Popular choices include mahogany, walnut, cherry, oak, and teak, each offering unique aesthetic and durability characteristics.
Can I insure my home’s luxury wood features?
Yes, many homeowner’s insurance policies cover damage to high-value materials, including luxury wood. Ensure you specify these features in your policy.
What are the warranty options for luxury wood products?
Warranty terms vary depending on the manufacturer and specific product. Always review the warranty details before purchase.